Ultrasonic technology has been widely used in metal, plastic welding process. Because of its high performance requirements on structural dynamics, the traditional design methods of imitation and mold repair can no longer adapt to the changeable requirements of plastic products. This paper starts with the principle of ultrasonic plastic welding, carries on the natural frequency and the modal analysis through the finite element method, designs the new tooling, meets the effective transfer and the uniform distribution vibration energy function requirements. In the design process in combination with ANSYS parametric modeling, the factor of design optimization of experiment (DOE) and the probabilistic design system (PDS) module, the parameters design and robust design, adjust the geometry size, make tooling and the inherent frequency of ultrasonic frequency match, the corresponding modal amplitude evenly in the face, reduce the local structure problem of stress concentration, At the same time, it has good adaptability to the changes of material and environmental parameters. The designed ultrasonic tools can be put into use after one processing, which avoids the waste of time and cost caused by repeated dressing tooling.
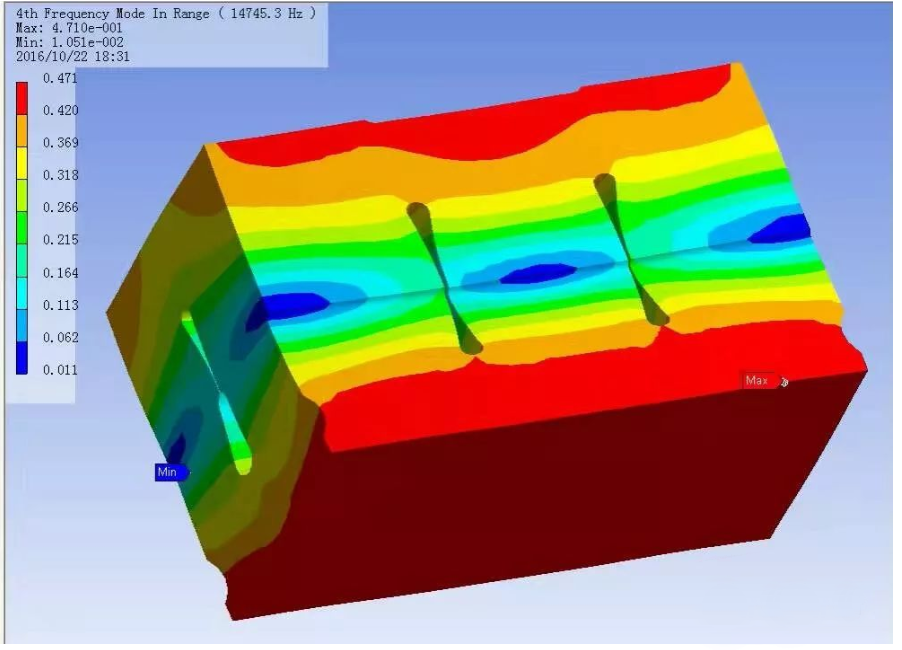
As the contact interface between the ultrasonic plastic welder and the material, the ultrasonic tool head's main function is to transfer the longitudinal mechanical vibration from the amplitude converter to the material evenly and effectively. The materials used are usually high quality aluminum alloy or even titanium alloy. Because the design of plastic materials changes, the appearance of thousands of different, the tool head will also change. The shape of the working face should be well matched with the material, so as not to damage the plastic when vibrating; At the same time, the fixed frequency of the first order longitudinal vibration should be coordinated with the output frequency of the welding machine, otherwise the vibration energy will be consumed internally. When the tool head vibrates, the local stress concentration will be generated. How to optimize these local structures is also a problem to be considered in the design. This paper discusses how to use ANSYS design tool head to optimize design parameters.
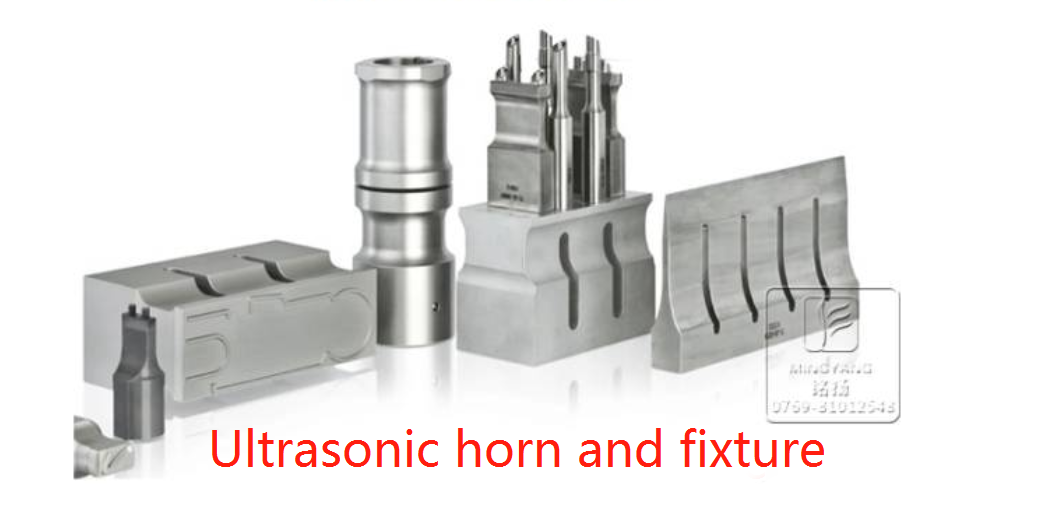
The design of welding horn and fixture are very important. There are many domestic ultrasonic equipment suppliers to produce their own welders, but a considerable part of them are imitation existing, and then constantly dressing tooling, testing, through this repeated adjustment method to achieve the purpose of tooling and equipment frequency coordination. In this paper, the finite element method can determine the frequency when designing the assembly. The error between the test results of the manufactured tooling and the design frequency is less than 1%. At the same time, this paper introduces the concept of DFSS (Design For Six Sigma) to optimize and Design the tooling robustly. The concept of 6-Sigma design is to fully collect the voice of customers in the design process to carry out targeted design; In addition, the possible deviation of the production process should be considered in advance to ensure that the quality of the final product is distributed at a reasonable level.
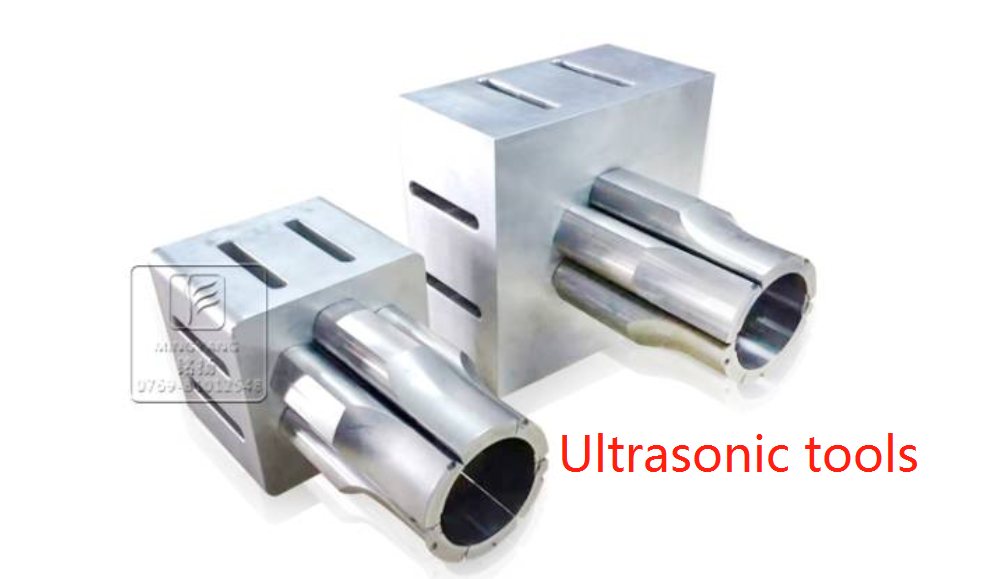
Post time: Sep-22-2022